Tata Tele Business Services offers best
solutions customized for your
Industry
Have one of our specialists reach out to you. Request a callback today!
Our Clients
From driving renewed value to embracing new technologies, we help our clients accelerate digital transformation and promote growth
Empowering Businesses with Solutions Crafted for Success
Find tailored solutions for your collaboration, communication, and connectivity needs - with services that push the limits and unfold new possibilities.
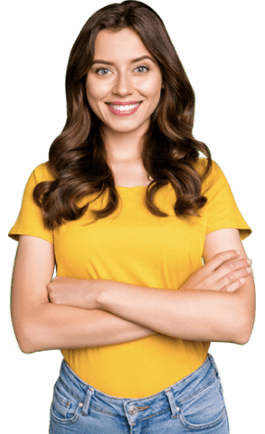
Got
questions?
Connect with us to find out which service works best for you.
Share your details and we will get in touch with you.
Your Questions, Answered
Our team walks the extra mile to ensure that you enjoy a smooth service. For any queries regarding service downtime and billing, email us at 1515@tatatel.co.in.
At TTBS, managing your account is simpler than ever. Click on the links below for more information:
Our team is here to support you, wherever life takes you. For queries on moving to a new location, please email us at 1515@tatatel.co.in
We understand the unique needs of our customers and are ever ready to customise our services to match them. Kindly mail your requirements to dobig@tatatel.co.in and our representatives will offer the best service plan to suit your needs.
Our customers are at the heart of our business. That’s why we offer you a range of benefits that can impact your business positively.
Click on the below benefits to know more about how you can make the most of TTBS:
We consistently improve our services to match the needs of our customers like you. To sign up for a new service, request a callback.
We are always seeking talented professionals who can drive our business forward. Please visit our careers section to learn about our open positions.
To get your queries about PF and Gratuity resolved, please reach out to subhash.aakre.ernst@tatatel.co.in
We will be delighted to have you as one of our investors. Kindly mail your investment details to investor.relations@tatatel.co.in and our representative will connect with you at the earliest.
We have immense respect for the investors who have believed in us and our company. Kindly share your queries at investor.relations@tatatel.co.in and our representative will respond at the earliest.
We ensure that our investors are updated on every aspect of our business growth. Kindly click here, to view Annual Reports for Tata Teleservices Limited and click here to view annual reports for Tata Teleservices Maharashtra Limited.
We ensure that we walk hand in hand with our Channel Partners to achieve mutual growth. Kindly mail us your queries at partner.connect@tatatel.co.in and our representative will respond with a resolution at the earliest.
We understand that promoting your business is vital for business expansion and we are happy to be with you in your journey. To view the different sales and marketing material, click here >>
We look forward to create a network of Channel Partners to build a more connected business community. To join our ever-growing network of Channel Partners, click here >>